Slashed Detection of Manufacturing Inefficiencies from Days to Seconds
Detecting cardboard quality deviations in near real time enables MM Karton to produce the highest quality product at an optimum price.
Self-Service Data Intelligence for Non-Technical Users
Kibana empowers machine operators with new insight into cardboard product KPIs such as chemical, moisture and other quality measures.
Optimizing Usage of Raw Materials
Within four months, MM Karton lowered consumption of high-cost materials during production by 20% with same output.
Production Efficiency Keeps Costs Low
Efficient use of materials and improved production speed leads to significant cost savings.
Company Overview
The Mayr-Melnhof Group is the market leader in cartonboard production and processing and holds a unique position in Europe. A comprehensive portfolio as well as broad geographical presence provide balance and potential. Founded in 1950 and based in Vienna, Austria, the multinational company is 57% family owned and since 1994, listed on the Vienna Stock Exchange.
MAYR-MELNHOF KARTON’S JOURNEY WITH ELASTIC
Mayr-Melnhof Karton: Powering the Search for Real-Time Costing
The Mayr-Melnhof Group has two business units. Mayr-Melnhof (MM) Karton is the world’s largest producer of coated recycled fiber-based cartonboard with a significant position in virgin fiber-based cartonboard. With an annual production capacity exceeding 1.7 million tons, approximately 80% is accounted for by recycled fiber-based cartonboard and approximately 20% by virgin fiber-based cartonboard.
As the leading producer of folding cartons in Europe and one of the largest producers worldwide, MM Packaging processed around 767,000 tons of recycled and virgin fiber-based cartonboard into around 63 billion consumer goods packages in 2017, alone. The comprehensiveness of their product offerings, from production to packaging, is central to Mayr-Melnhof Group market leadership.
To meet their high standards as a best-in-class provider, MM Karton is constantly innovating technical capabilities – including on the shop floor, where optimizing the production efficiency of cardboard translates into the highest quality product at the lowest cost.
Being a market leader means being a tech leader. Our ability to quickly detect deviations in the manufacturing process and adjust on the fly is a competitive advantage.
Visibility into Complex Manufacturing Processes
The production of cardboard requires a complex manufacturing process – the amount of moisture, fiber, and expensive materials required for each batch needs to be precise. When the quantities are just right, the company can produce a high-quality product at an optimum price. When the recipe is off, quality and cost both suffer.
In the past, discovering deviations in a batch of virgin fiber-based cardboard could take an hour or even days; by the time they realized something had gone wrong, it was too late to recover the batch. If they were running a test batch to try a new grade on an existing product, for example, the manufacturing process would halt as they waited for quality test results from the lab, leading to lost time and materials.
The biggest hurdle to closing this time gap was a fragmented infrastructure. Every step of the cardboard manufacturing process has its own OT system (Operational Technology), sensors, and measurement. Over 25,000 sensors capture production process data on everything from pressure and temperature to machine speed and power consumption. MM Karton was producing plenty of data – 2 TB – but they lacked the right tools to get intelligence out of disconnected process control systems and make the data actionable for operators.
When There's a Vision, There's a Way
Process Technologist Stephan Hampe is responsible for optimizing manufacturing processes and creating cost-saving measures across seven of MM Karton’s plants. Following a big data analytics presentation for all heads of staff in the cardboard mills, Stephan was inspired and crafted a clear vision: to connect and visualize cardboard production data and usage of all relevant materials in one dashboard, in real time.
He took his vision to Head of Operations Jürgen Kerner. Said Jürgen: "Everything started with Stephan’s appeal that it couldn’t be that hard in the year 2017 to have a time-series visualization. I simply said ‘challenge accepted’ and ‘let’s do it with Elastic.’ I knew it was possible, but I just hadn’t planned on it being such a success story so quickly."
Committed to open source technology and already familiar with the Elastic Stack, Jürgen knew it could be the perfect means to deliver on Stephan’s vision. Jürgen used Elasticsearch at a previous company as a data store for financial information. At MM Karton, he was already using the Elastic Stack for log analysis, and had recently purchased a subscription, gaining access to and advantages of commercial features of the Elastic Stack, such as auditing, for a regulatory use case.
As part of their due diligence, Jürgen and his team explored other options to get real-time visibility into the manufacturing process, but cost was an issue. One of the biggest IT and professional services providers in Europe suggested a proprietary ERP specialized solution for the cardboard industry – but at ten times the cost and significantly fewer capabilities, it paled in comparison to the Elastic Stack. Other well-known options had a poor user experience and relied on Excel to handle time-series data – a cumbersome approach degrading speed of development – they refused to take.
It came down to ease of use and elegance. Kibana would make it possible for non-technical users including electrical, automation, and maintenance engineers to easily create dashboards and visualize data.
"Stephan is a cardboard maker, not an IT guy," said Jürgen. "He knows how to use technology but he’s not a fiend with graphs. Yet it’s still so easy for him to create his own dashboards. Once he got Kibana, he was able to create and visualize everything he ever dreamed."
To Understand a Process, You Have to Visualize It
Within five weeks, Stephan had learned how to use Kibana and produced dashboards with dozens of graphs.
You cannot understand a process if you do not visualize it. I realized that we needed to marry all the systems together, pull the main parameters from the process systems, databases, and other sources, and see them together in one place.
MM Karton first ingests data from multiple sources (PLC Systems), including SQL databases and machine sensors, uses a homegrown system to ship data to Logstash, then stores it in Elasticsearch. The real-time process data is then matched with recipe data and an Internal Material Costing (IMC) formula created by Stephan and his team, which provides insight into the usage costs of the raw materials. They are able to know whether they are over, under, or right on track.
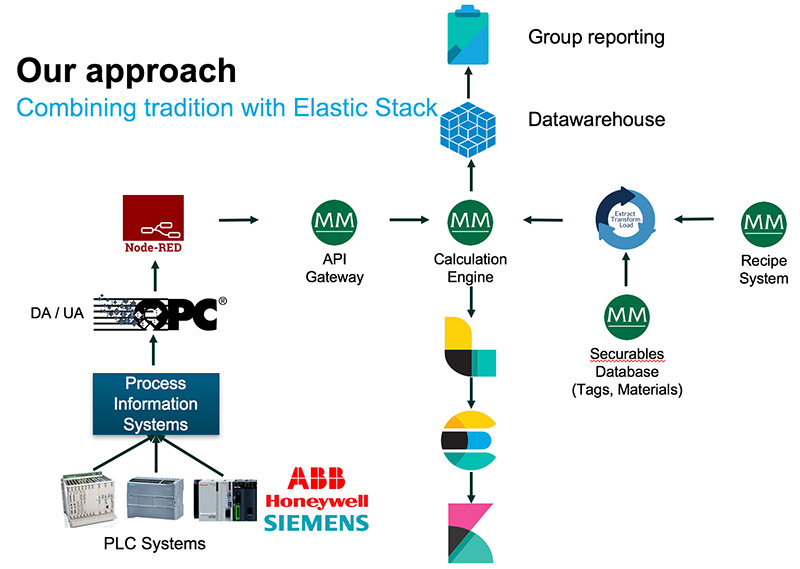
Real-time process monitoring with the Elastic Stack delivered on MM Karton’s goal to visualize and optimize the cardboard making process.
"The Elastic Stack makes sense of otherwise disparate data, bringing in a new real-time perspective on production processes," said Stephan. "With one feature set, we're able to bridge the two worlds of IT and OT, and optimize the process."
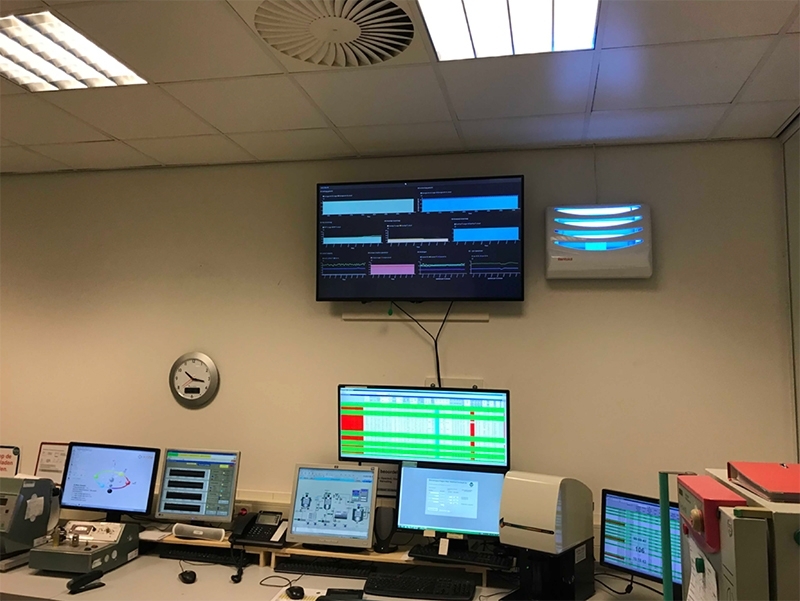
View of the production process via Kibana dashboards in the control room.
MM Karton is currently piloting the Elastic Stack to visualize cardboard production across seven plants, with rollout planned for all plants by the next two years.
Real-time costing is similar to what’s happening in financial trading. We’re taking a high-stakes use case from the financial services industry and applying it to a production use case on the shop floor to drive significant cost advantages.
Visualization: The Language of the Shop Floor
According to Jürgen, originally the process production teams didn’t want to deal with technology because they assumed it would be complicated, but Kibana won them over. With an introduction of a mere two hours, they are able to create their own charts, graphs and data visualization without any help. These dashboards have transformed how operators monitor production materials and benchmarks.
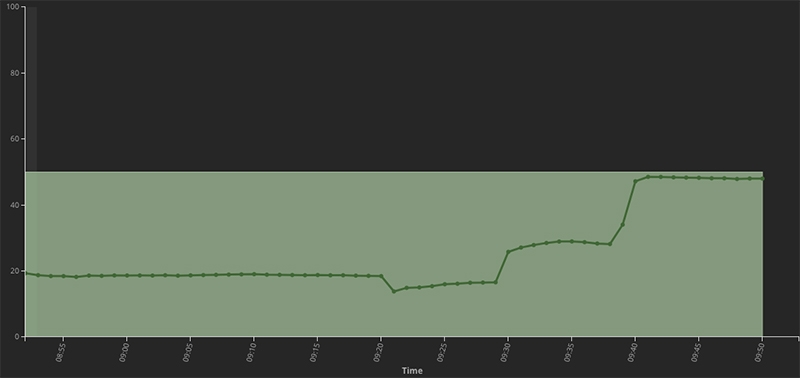
Kibana is used to manage material quantities over time.
Value for Users from Shop Floor to C-Suite
Jürgen thinks working with Elastic is different from other vendors that require significant up-front development and still fall short of requirements. Instead, the relationship with Elastic is built on proven technology, results and trust. And early on, he knew they made the right choice.
"I remember the exact date," he said. "I was at Elastic{ON} San Francisco 2018 when I heard from Stephan that he had made his first valid Kibana dashboard. In that moment, instead of the Elastic Stack belonging to IT, it became the shared path for everyone to get the real-time insights they wanted."
While the majority of legacy production and automation systems weren't built with user-centered design, Kibana's intuitive interface has created a new data discovery model, enabling self-service data intelligence.
Even MM Karton's Managing Director envisions using Kibana as an enterprise bridge to visualize data across all machines and production processes. Canvas will allow Jürgen and his team to create dynamic presentations that pull live data directly from Elasticsearch, further simplifying mill management and consumption of data for a broad range of users, from the shop floor to the C-suite.
Reusability is key; now that MM Karton has the Elastic Stack for this use case, it's easy to add data from more sensors and systems (e.g., lab, quality control, etc.) to fulfill other needs, such as quality control of raw materials and use cases beyond production (e.g., finishing and cutting cardboard). Over time, MM Karton plans to introduce alerting functionality to further optimize supply chain processes and tap into machine learning for analysis of critical process conditions.
High Efficiency and Clear Insight
Thanks to clear insight into production processes and usage of materials, MM Karton has already improved its recipes to lower the amount of expensive ingredients. When materials can cost upwards of €15,000/ton, a net increase or decrease of 10 tons per year can have a major impact. In less than four months, they reduced consumption of one expensive material by 20%, while still maintaining the same output.
The company has also improved production speed without sacrificing quality. "If you can get one meter more per minute on a production cycle of 24 hours, that’s a huge amount of cardboard that can be brought to the market," said Jürgen.
Also, by using the Elastic Stack to visualize and optimize the process of cross cutter machines (to cut out sheets from rolls of cardboard), one mill has eliminated the need for storage.
"It's quickly become clear for everyone that visualization is a must," said Jürgen. "Real-time analysis and visualization is what brings the whole manufacturing process forward."
Deployment Statistics
- Number of Clusters3
- Number of Nodes12
- Number of LS instances/Beats12
- Total Number of Documents3.5 billion
- Total Data Size2 TB
- Daily Ingest Rate1 GB
- Number of Indexes3
- Query Rate10/s
- Node Specifications:Hot, warm deployment
Hot: physical nodes with 64GB RAM, 8 core CPU, SSDs
Warm: VM’s with 64GB RAM, 8 Cores, HDDs