品質検査を数日から数秒へ短縮して効率化
ボール紙品質の誤差をほぼリアルタイムに検出することにより、適切な価格で最高品質の製品を製造
広範なユーザーのためのセルフサービスデータインテリジェンス
Kibanaが化学物質や水分、その他の品質測定をはじめとするKPIのインサイトを提供してボール紙製造の機械オペレーターをサポート
原料の使用を最適化する
導入から4か月以内に、同じ生産量を維持しながら高コスト原料の消費を20%削減
生産効率を高めてコストを下げる
原料の効率的な使用と生産速度の向上で大幅なコスト低下を実現
マイヤー・メルンホフ・カルトンについて
ボール紙製造・処理の最大手、マイヤー・メルンホフ・グループは欧州でも独自の存在です。包括的なポートフォリオと広範な地理的プレゼンスを有し、資産と成長率の双方を兼ね備えています。57%が家族保有の多国籍企業として1950年にオーストリア・ウイーンで創業の後、1994年にウィーン証券取引所に上場しました。
マイヤー・メルンホフ・カルトンのElastic Stackストーリー
マイヤー・メルンホフ・カルトン:検索が支えるリアルタイムなコスト削減
マイヤー・メルンホフ・グループには2つの事業ユニットがあります。マイヤー・メルンホフ・カルトン(MMカルトン)はリサイクル繊維塗工紙製造の世界最大手であり、またバージンファイバーボール紙で大きく躍進しています。170万トンを超える年間生産能力の約80%をリサイクル繊維塗工紙が占め、20%ほどをバージンファイバーボール紙が占めます。
MMパッケージングは段ボール製造で欧州首位、世界でも最大手の一角を占め、これまでに76万7千トンのリサイクルおよびバージンファイバーボール紙を取り扱い、630億点のコンシューマー用品パッケージを製造してきました。このように製造からパッケージングまで広範な製品を供給する包括的な事業ポートフォリオは、マイヤー・メルンホフ・グループが市場を牽引する基盤となっています。
業界屈指のメーカーとして高い品質基準を満たすため、MMカルトンは継続的な技術革新に余念がありません。工場の製造現場における生産能力の最適化を、低コストで高品質な製品で実現する取り組みもその1つです。
市場でトップを保つには、技術でもトップに立つ必要があります。製造工程で誤差をすばやく検知し、即時に修正する能力は重要な競争力となります。
複雑な製造工程を可視化する
ボール紙製造の工程は非常に複雑です。すべてのバッチにおいて湿度、繊維、高価な原料が正確に基準を満たす必要があります。同社が適切な価格で高品質な製品を製造できるのは、分量が正確な場合だけです。製造規定を満たさない場合には、品質とコストの両方が犠牲になります。
かつてバージンファイバーボール紙の誤差を検出するためには、1バッチあたり1時間から数日程度かかっていました。しかも問題が検出された時点で、すでにそのバッチの品質を取り戻すことはできなくなっています。既存製品でテストバッチ、つまり、ラボでテスト結果がでるまで製造工程を停止するなどの新しい評価手法を実施できれば、時間や原料のロスの削減につながります。
この時差をなくすにあたり最大の課題となったのが、細分化されたインフラの壁でした。ボール紙の各製造工程には、それぞれ独自のOT(オペレーショナルテクノロジー)システムとセンサー、測定基準があります。圧力や温度、さらにマシンのスピードや電力消費量まで、2万5千を超えるセンサーがあらゆる製造工程データを計測しています。実際にMMカルトンでは2TBという大量のデータが生成されていました。ただ欠けていたのは、接続されていない工程制御システムからインテリジェンスを抽出し、オペレーターが実践可能なデータを作成するツールだったのです。
ビジョンがあれば、道はひらける
ステファン・ハンプ氏は工程技術者として、MMカルトンの7つの工場で製造工程の最適化とコスト削減手段を担当しています。ハンプ氏はあるとき工場で責任者を対象に実施されたビッグデータ分析プレゼンテーションに参加し、それをきっかけにある明確なビジョンを抱くようになりました。すなわち、ボール紙の製造データと全原料の使用状況をすべて関連付け、リアルタイムに1つのダッシュボードで可視化するというアイデアです。
ハンプ氏はオペレーション責任者のユルゲン・ケルナー氏にこのアイデアを伝えました。ケルナー氏は当時について次のように振り返ります。「2017年内に時系列データを可視化することは難しくないはずだ、というステファンの提案からすべてがはじまりました。私は『挑戦しよう』、『Elastic製品で行こう』とだけコメントしました。 不可能とは思いませんでした。ただ、これほど早くすべてがうまくいったのは嬉しい誤算でした」
オープンソーステクノロジーの知見があり、Elastic Stackにも精通していたケルナー氏は、ハンプ氏のビジョンを実現する上でElastic Stackが最適だと判断しました。ケルナー氏は以前の職務で財務情報のデータストアにElasticsearchを使用していました。MMカルトンに参加してからはログ分析にElastic Stackを使っており、さらにサブスクリプションを開始して法規制関連の監査などに有償オプションを活用しはじめたところでした。
ケルナー氏のチームはデューデリジェンスの一環で製造工程のリアルタイムな可視化のさまざまなオプションを検討しましたが、問題は費用でした。ある欧州最大のIT/法人向けサービスプロバイダーの提案はERPに特化した商標登録製品によるソリューションでした。しかしElastic Stackと比較すると費用は10倍、一方で機能の数は劣ることがわかり、導入は見送られました。もう1つ、よく知られた選択肢として、時系列データをExcelで扱うという方法もあります。ユーザーエクスペリエンスの満足度も低く、開発スピードを低下させる厄介なアプローチであることから、こちらも見送られました。
つまり、使いやすさと簡潔さが重要です。Kibanaは電気系や自動化、メンテナンス関連の技術者を含め、ITエンジニアではないユーザーにとって使いやすく、ダッシュボードの作成やデータの可視化も簡単に行うことができます。
ケルナー氏は次のように語ります。「ステファンは製造管理が専門で、IT畑の出身ではありません。技術的な知識はありますが、グラフ作成は専門外。しかし彼にとってKibanaはとても簡単で、独自のダッシュボードをすぐに作れます。Kibanaを手にしたことで、ステファンは望んでいた通りすべてを可視化できるようになりました」
工程理解のための可視化
ハンプ氏は5週間でKibanaの使い方を習得し、いくつものグラフを表示するダッシュボードを完成させました。
可視化しない限り、工程を理解することはできません。すべてのシステムを関連付ける必要があるとわかりました。工程システムやデータベース、その他のソースから主要なパラメーターを抽出し、1か所に表示させるのです。
同社ではまず、自社システムを使用してSQLデータベースやマシンのセンサーを含む複数のソース(PLCシステム)からLogstashにデータをシッピングし、その後Elasticsearchに格納するという方法でデータを投入しました。次にリアルタイムな工程データを製造マニュアルのデータ、およびハンプ氏とチームが作成した社内向けの原料コスト計算式と比較します。これにより、原料の使用コストに関するインサイトを得ることができます。多すぎたり、不足している、あるいは適量といった結果が出力されます。
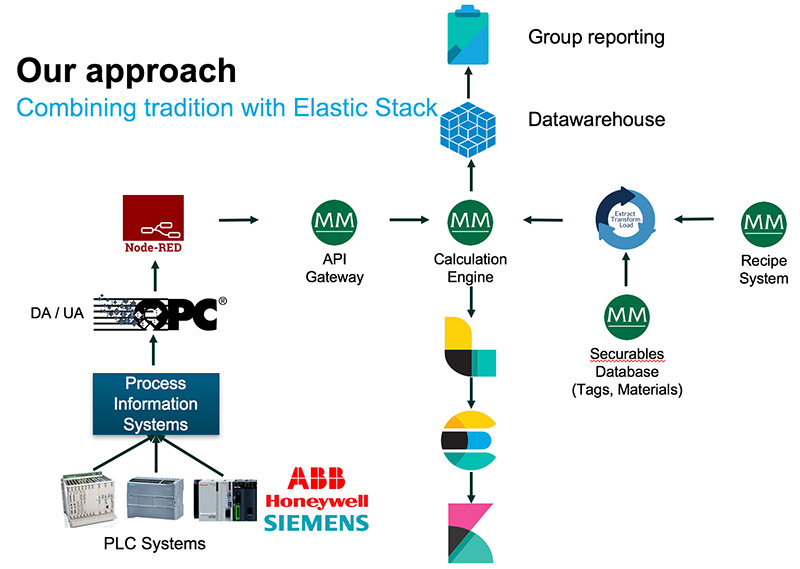
MMカルトンがElastic Stackでリアルタイムな工程監視を行う狙いはボール紙製造工程の可視化と最適化です。
ハンプ氏はこう述べます。「まったく異種のデータ同士を扱えるElastic Stackは、製造工程に新しいリアルタイムな視点をもたらします。この機能性が、ITとOTという異なる世界に橋を架け、工程を最適化するのです」
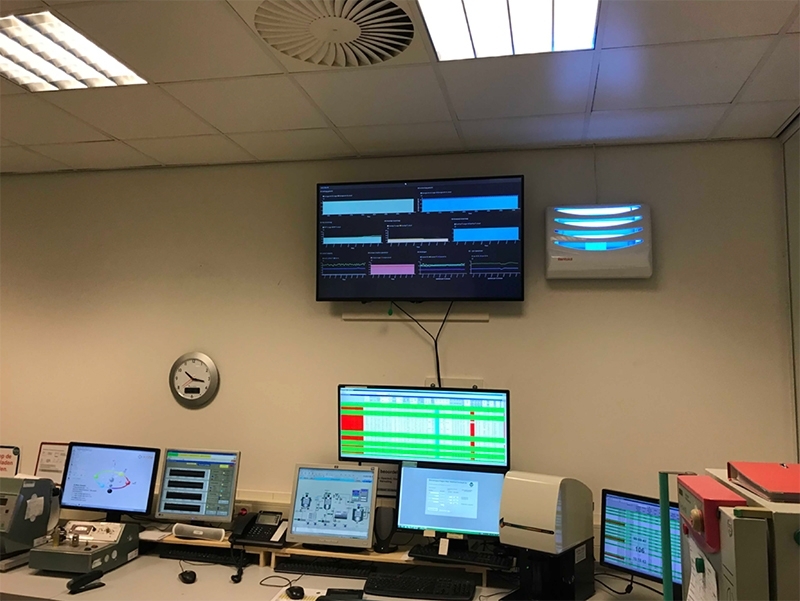
制御室で使用されている、Kibanaを用いた製造工程ダッシュボード
MMカルトンは現在7つの工場でElastic Stackを使った可視化を行っており、さらに今後2年以内に全工場への水平展開を予定しています。
リアルタイムなコスト管理は金融取引に使われる手法と似ています。私たちは金融業界の手法を製造業のユースケースに、現場レベルで導入するという大きな懸けに出ました。その結果、顕著なコスト競争力を生み出しました
可視化:現場の反応
ケルナー氏によると当初、工程管理チームはテクノロジーに対して否定的でした。"ややこしく、扱いづらいものだろう"という彼らの先入観を覆したのがKibanaです。チームは導入説明からわずか2時間で、オリジナルのチャートやグラフ、データ可視化を一切のサポートなしに作れるようになりました。ダッシュボードの導入により、オペレーターが製造原料とベンチマークを監視する方法も変化しました。
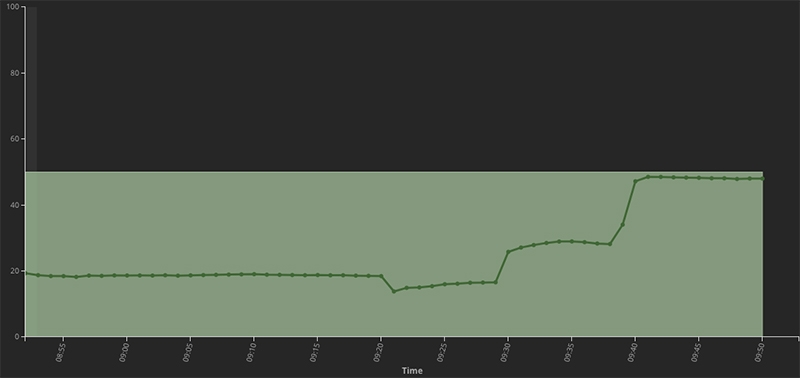
やがてKibanaは、原材料の使用量管理にも使われるようになりました。
工場現場から経営陣まで使用
ケルナー氏は、Elastic製品の導入エクスペリエンスは他のベンダーとまったく異なると指摘します。他のベンダーでは膨大な事前開発が必要な上、機能的には劣ることがほとんどだからです。さらにケルナー氏は確かな技術、結果、信頼がElasticとの関係性を築くと言います。彼は"Elastic Stackを選んだのは正解だ"と導入の初期段階から確信していました。
「正確な日付まで覚えています。2018年、サンフランシスコでElastic{ON}に参加している最中にステファンから『Kibanaダッシュボードの第1号が完成した』と連絡が来ました。あの瞬間、Elastic StackはIT業界だけのものではなくなりました。リアルタイムにインサイトを求めるすべての人に開かれた技術になったのです」
レガシーな製造システムや自動化システムの多くはユーザー中心の設計で構築されていません。しかしKibanaの直感的なインターフェースから新しいデータディスカバリーモデルが生まれ、データインテリジェンスをセルフサービスで利用できるようになりました。
現在、MMカルトンの管理部長はすべての機械と製造工程のデータを可視化する架け橋としてKibanaを使うビジョンを描いています。新たにCanvasを使えば、ケルナー氏のチームはElasticsearchから直接ライブデータをプルし、動的なプレゼンテーションを作ることが可能になります。工場管理だけでなく、現場から経営陣までの幅広いユーザーを対象とするデータ表示もよりシンプル化することができます。
カギは"再利用性"です。より多くのセンサーとシステム(ラボや品質管理など)からデータを追加することで、現在MMカルトンでは原料の品質管理や製造以外のユースケース(ボール紙の仕上げやカッティング)といったニーズにも簡単にElastic Stackを活用できるようになりました。同社では今後、通知機能によるサプライチェーンプロセスの最適化や、機械学習を活用した重要工程の状況分析の導入を計画しています。
優れた効率と明確なインサイト
製造工程と原料の使用状況に関する明確なインサイトを得たMMカルトンは、高コスト原料の配合を抑える改善を実施しました。原料1トン当たりの価格は最大で1万5千ユーロ(約187万5千円、レート1€=125円の場合)と高価であることから、年間10トンの上下でも大きな影響が生じます。導入から4か月以内に、同じ生産量を維持しながら高コスト原料の消費を20%削減させました。
さらに同社は品質を損なうことなく、生産ペースの引き上げにも成功しました。ユルゲン・ケルナー氏は次のように指摘します。「24時間の製造サイクルで1分あたりの生産量をあと1メートル増やすことができれば、市場に届くボール紙の量も大幅に増えます」
さらにElastic Stackを使用した可視化でクロスカッターマシン(ボール紙のロールからシートを裁断する機械)の工程が最適化され、ある工場では保管スペースの圧縮も実現しました。
ケルナー氏は「まもなく、可視化は欠かせないと全員が気付きました。製造工程を進化させたのは、リアルタイム分析と可視化です」と述べます。
デプロイの詳細
- クラスター数3
- ノード数12言語
- LS/Beatsインスタンス数12言語
- ドキュメント総数35億
- 総データサイズ2 TB
- 投入レート(1日あたり)1 GB
- インデックス数3
- クエリレート10/秒
- ノードの仕様:Hot-Warmデプロイ
Hot:物理ノード(64GB RAM、8コアCPU、SSD)
Warm:仮想マシン(64GB RAM、8コアCPU、HDD)